If you choose a reinforcing material as the filling material of superhard resin abrasive tools, which materials will you think of? May think of: copper powder, silver powder, aluminum powder, cobalt powder, zirconium powder, copper-tin alloy powder and other metal powder; Zinc oxide, chromium oxide, calcium oxide, magnesium oxide and other alkali metal oxides; Silicon carbide, white corundum and other common abrasives; Cryolite, fluorite, zinc sulfide, pyrite and other active fillers; Polytetrafluoroethylene, molybdenum disulfide, flake graphite and other fillers with certain lubricating properties; There's so much variety! Don't worry, we may wish to think about the next kind of reinforcement effect is better superhard resin abrasive filler should have what performance. Let's get our ideas straight: First, the reinforcement effect is good. This is the basic functional requirement. From the reinforcement effect, copper powder, cobalt powder, silver powder and other metal powder reinforcement effect is the best. Among them, copper powder and bisimide resin powder are chemically adsorbed, and the strength is better. Followed by silicon carbide, white corundum and other common abrasives and zinc oxide, chromium oxide and other alkali metal oxides. Among them, the reinforcement effect of silicon carbide powder is better, because it is easier to be wet by the resin. The reinforcing effect of active fillers such as cryolite and fluorite is poor, and the reinforcing effect of lubricating fillers such as polytetrafluoroethylene, molybdenum disulfide and flake graphite is even lower, which is basically excluded. Second, the particle size is controllable. Particle size is controllable, including the size and distribution of particle size is controllable, and the wider the particle size, the better, which is conducive to the selection of different particle sizes to match different particle sizes of grinding wheels. As a binder, in principle, the finer the particle size, the better, but the particle size is too fine, mixing will become very difficult. A selection criterion here is that the size of the binder does not exceed one-third of the size of the abrasive. This is not only conducive to the strength of the binder holding the abrasive, but also conducive to mixing.
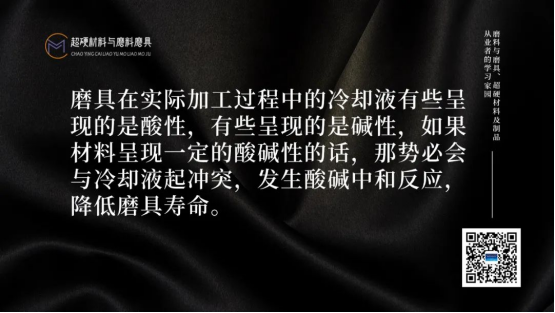
In terms of chemical properties, the best is silicon carbide, white corundum and other ordinary abrasives. They generally do not react chemically with other materials and have good stability. Metal powders such as copper powder and alkali metal oxides such as zinc oxide and chromium oxide will neutralize with acid in an acidic environment, which will lead to a decrease in the life of abrasive tools. Among them, zinc oxide, chromium oxide and other alkali metal oxides are more prone to chemical reactions, and special attention should be paid to them. Fifth, the heat conduction coefficient is high, the conduction effect is good. Resin abrasive because the resin is not resistant to high temperature resulting in low grinding wheel life, if the heat conduction of the filler is good, it can instantly transfer a lot of heat, which will increase the life of the resin abrasive.
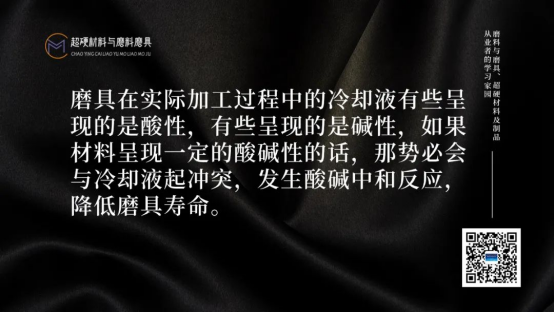
From the perspective of heat conduction, the heat conduction effect of metal powder such as copper powder is the best, the heat conduction coefficient is generally greater than 200W/(m*k), high efficiency, fast speed, no problem. The heat conduction effect of flake graphite is second only to that of metal powder such as copper powder, and the heat conduction coefficient reaches 110-190W/(m*k), but it is eliminated due to the poor reinforcement effect discussed in this discussion. The heat conduction of ordinary abrasives such as silicon carbide and white corundum ranks in the third echelon, belonging to the middle and upper level. Among them, the thermal conductivity of silicon carbide is 83.6W/(m*k), second only to copper powder and other metal powders and graphite. Sixth, the coefficient of thermal expansion is low. If the coefficient of thermal expansion is high, the packing may crack when it is heated to a certain extent during the grinding process. In terms of thermal expansion coefficient, silicon carbide and white corundum belong to the first echelon. Among them, the thermal expansion coefficient of silicon carbide is 4.5*1E-6 /K, which is the closest to diamond 1.2-4.5*1E-6 /K. Followed by zinc oxide, chromium oxide and other alkali metal oxides, of which magnesium oxide thermal expansion coefficient is the best, 13*1E-6 /K, others are generally greater than 15*1E-6 /K. The second is copper powder and other metal powder, of which the thermal expansion coefficient of aluminum powder is 20~29.9*1E-6 /K, and the other is generally greater than 30*1E-6 /K. Seventh, the shape is controllable, can not flake too much. Too much flake is bound to cut off the resin cross-networking structure, which is not conducive to the strength of abrasive tools. Obviously, this article is tailored for flake structural materials such as flake graphite, and once again the flake materials such as flake graphite are eliminated. Eighth, a wide range of sources, affordable. In terms of source and price, silicon carbide, white corundum and other common abrasives and zinc oxide, chromium oxide and other alkali metal oxygen